Accelerating Smart Manufacturing Through Artificial Intelligence-Driven Predictive Maintenance
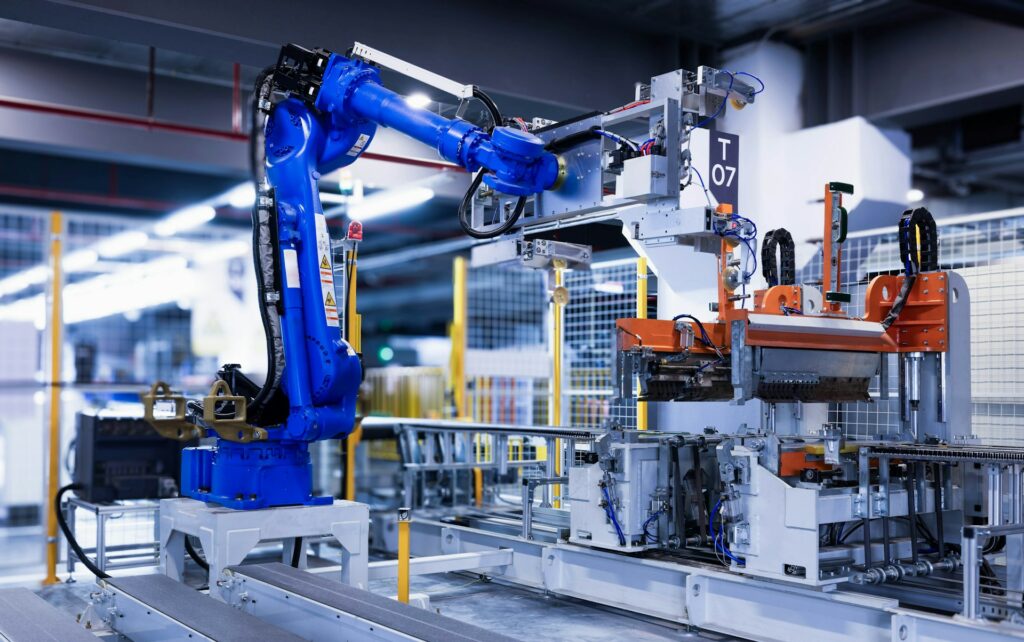
Accelerating Smart Manufacturing Through Artificial Intelligence-Driven Predictive Maintenance
Picture a modern factory floor: robotic arms moving in perfect rhythm, machines humming in controlled harmony, and data silently flowing from every sensor and motor. However, behind this intricate dance is a strong brain that not only ensures that everything continues to function normally, but also anticipates potential problems before they really occur.
This is the kind of potential that artificial intelligence-driven predictive maintenance holds, a technology that is quietly changing manufacturing into something that is more intelligent, quicker, and more robust than it has ever been.
Examining the Reasons Why Traditional Maintenance Is Not Enough Beyond Routine Checks
Over the course of many decades, factory maintenance adhered to a straightforward principle: either examine machinery on a predetermined timetable or wait until they broke down. While this approach sounds practical, it often leads to two big problems. In the first place, it results in unneeded downtime when components that are in fine condition are changed too soon. Second, it fails to prevent sudden breakdowns that halt production lines, disrupt supply chains, and cost companies millions.
This is where predictive maintenance changes the game. Instead of relying on guesswork or rigid schedules, factories can now use real-time data and AI algorithms to detect tiny shifts in machine behavior long before a failure occurs.
How Artificial Intelligence (AI) Gives Machines a Voice
When it comes down to it, predictive maintenance is all about providing machines the capacity to communicate with one another. Sensors capture data like vibration, temperature, pressure, and sound. This set of figures is nothing more than raw facts on its own. But when AI steps in, patterns begin to emerge.
Machine learning models can spot subtle signs of wear that human eyes and ears might miss — perhaps a barely noticeable increase in vibration or a slight temperature rise. Over time, AI becomes better at understanding what normal operation looks like and what might signal an impending problem.
The result? Maintenance teams get alerts days or weeks before a component fails. They can schedule repairs during planned downtime, keeping production lines running smoothly.
The Ripple Effects: Efficiency, Cost Savings, and Sustainability
The benefits of AI-driven predictive maintenance extend far beyond avoiding breakdowns. By minimizing unexpected downtime, factories operate more efficiently. Machines last longer because parts are only replaced when truly needed, which also means less waste and lower inventory costs.
There’s also an environmental upside. When machines run in optimal condition, they consume less energy and produce fewer defective products. For manufacturers facing increasing pressure to cut carbon emissions, these savings matter — both financially and ethically.
Smart Factories and the Future of Manufacturing
Predictive maintenance is part of a larger movement toward smart manufacturing, where factories become connected, data-driven, and increasingly autonomous. In a smart factory, AI doesn’t just monitor equipment. It helps manage inventory, optimize production schedules, and even assist human operators in real-time decision-making.
Imagine a production line that knows exactly when to slow down, speed up, or pause for a quick tune-up — all without human intervention. This vision is becoming reality thanks to AI and the Industrial Internet of Things (IIoT).
Challenges Along the Way
Despite its promise, implementing AI-driven predictive maintenance isn’t always straightforward. Older equipment may lack built-in sensors. Collecting and cleaning large amounts of data can be complex. And machine learning models need time to “learn” what normal operations look like before they can accurately predict failures.
Moreover, success often requires cultural change. Maintenance teams must trust AI insights and adjust workflows accordingly. But for manufacturers willing to invest in these changes, the payoff can be transformative.
A New Era of Intelligent Maintenance
In the past, factories relied on routine checks and human intuition to keep machines running. Today, AI makes it possible to shift from reactive to proactive maintenance — catching problems early, improving safety, reducing costs, and keeping production lines moving.
It’s a quiet revolution happening behind factory walls, but its impact is huge: from the tiniest gear to entire global supply chains, AI-driven predictive maintenance is reshaping how things are made.
And this is only the beginning. As AI models become smarter and IIoT technology spreads, manufacturing will become more connected, efficient, and resilient than ever before — truly entering the age of intelligent industry.