An Artificial Intelligence-Driven Predictive Maintenance System That Reduces Manufacturing Downtime and Costs
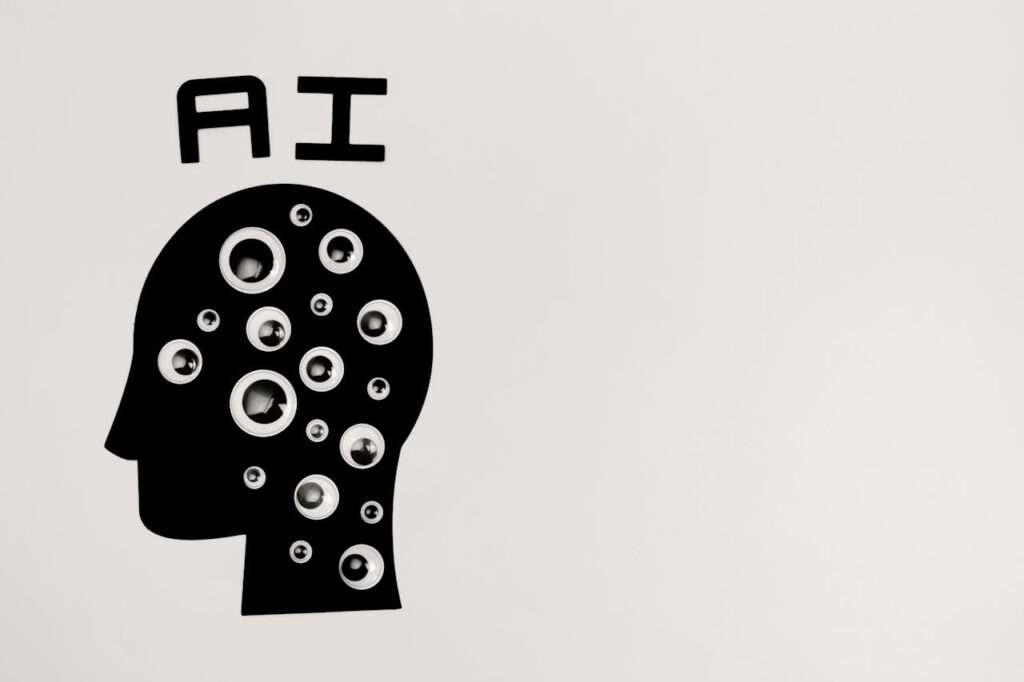
An Artificial Intelligence-Driven Predictive Maintenance System That Reduces Manufacturing Downtime and Costs
Every minute is important in the current industrial industry, which moves at a breakneck speed. When a single unexpected failure occurs on the production floor, it not only brings machines to a complete standstill, but it also has the potential to interrupt whole supply chains, cause deliveries to be delayed, and significantly increase operating expenses overall. Over the course of many decades, manufacturers have either depended on scheduled maintenance plans or responded to problems individually as they occurred. However, artificial intelligence is now responsible for rewriting that tale. Manufacturing facilities are now able to anticipate issues before they occur, therefore minimizing downtime, extending the life of equipment, and changing maintenance from a cost center into a competitive advantage. This is made possible by artificial intelligence-driven predictive maintenance tools.
The Reasons Why Manufacturing Requires a Creative Approach
Preventive and reactive maintenance tactics are the two types that are most often used in traditional maintenance. In accordance with the instructions provided by the manufacturer or the historical failure rates, preventive maintenance is planned at certain intervals. In spite of the fact that this may avoid some problems, it also results in the replacement of parts that are not essential and does not detect failures that occurred unexpectedly in between inspections. The opposite of preventative maintenance is reactive maintenance, which is conducted only after something has broken. This kind of maintenance often results in longer production stoppage and greater expenditures.
Predictive maintenance that is driven by artificial intelligence adds a new layer that is driven by data to this procedure. Artificial intelligence algorithms are able to find early warning indications that human operators or conventional techniques could overlook. This is accomplished by evaluating data from sensors that work in real time and learning from the performance of equipment in the past. This means that manufacturers are only able to take action when data suggests that there is a genuine danger, as opposed to waiting for something to break or replacing components that still have some life remaining in them.
How Artificial Intelligence Can Predict Failures Before They Occur
Data, and enormous amounts of it, is the foundation upon which predictive maintenance is built. Internet of Things sensors are often installed in modern industrial equipment. These sensors continually detect a variety of parameters, including temperature, vibration, power usage, pressure, and more. By processing this data, artificial intelligence systems search for subtle patterns and correlations that are associated with certain forms of wear or failure.
In the case of bearing degeneration, for instance, a modest increase in motor vibration accompanied with a slight rise in temperature can be indicative of the situation. Rather of relying only on predetermined criteria, the artificial intelligence learns, over the course of time, what constitutes “normal” for each given machine and what kinds of changes typically precede failures. Because of its flexibility to adapt, artificial intelligence is far more accurate than rule-based systems that are fixed, which may either fail to recognize issues or generate false alarms.
There is less downtime, which results in lower costs and a longer life for the equipment.
Manufacturers may avoid abrupt stoppages that might cost hundreds or even millions of dollars each hour, depending on the industry, by acting before problems occur and preventing them from really occurring. The disruption caused by planned maintenance during scheduled downtimes is less severe and more cost-effective than the cost of emergency repairs.
Another benefit of predictive maintenance is that it helps prolong the amount of time that costly gear may be used. Parts are only changed when they are required, which helps to reduce waste and cut the expenses associated with maintaining spare parts inventory. This is done rather than changing components based purely on the hours of operation or calendar schedules.
Aside from the financial benefits, this technique also enhances the safety of the workplace. It is possible for accidents to occur as a result of malfunctioning equipment; eliminating these incidents keeps workers safer. In addition, manufacturers are able to keep their product quality at a higher level and their delivery times more constant when they have equipment that is more dependable.
Instances from Across the Manufacturing Floor
In a variety of industries, including the manufacturing of food and beverages as well as automobile assembly lines, predictive maintenance is already having an effect. Artificial intelligence has the ability to identify imbalances, misalignments, or minor vibrations in businesses that depend heavily on conveyors, robotic arms, and CNC machines. These vibrations might potentially indicate worn bearings or components that have been miscalibrated.
In manufacturing facilities for chemicals and pharmaceuticals, where machinery must function under high pressure or severe temperatures, artificial intelligence is used to monitor crucial variables in order to anticipate breakdowns that may potentially interrupt production or pose safety issues. Even in environments where the machinery may seem to be less complicated, such as the textile and packaging industries, predictive maintenance may assist prevent expensive stoppages during high-volume runs.
Beyond the Capability of Prediction: Intelligent Planning for Operations and Maintenance
AI’s function is not restricted to only identifying possible errors. Additional capabilities of predictive maintenance systems include the ability to prioritize which problems need urgent attention, plan repairs in order to minimize disruptions, and assist teams in more efficiently allocating resources.
These systems, throughout the course of time, acquire knowledge from each and every maintenance activity and outcome, hence enhancing their forecasts and suggestions. The whole maintenance process is made more intelligent as a result of this, which reduces the number of manual inspections and frees up qualified professionals to concentrate on more complicated repairs and enhancements to the process.
Opportunities for Adoption, as well as the Ways in Which Manufacturers Are Overcoming Them
The implementation of AI-driven predictive maintenance is not always straightforward, despite the fact that the advantages are obvious. Certain manufacturing facilities have older machinery that do not have contemporary sensors, which necessitates retrofitting. Collecting data of a high quality and ensuring that it is dependable is of the utmost importance; inaccurate data leads to inaccurate forecasts.
The construction of AI models also requires a level of knowledge as well as an awareness of certain equipment and procedures. There are a lot of manufacturers that begin on a modest scale, concentrating on their most important pieces of machinery, and then gradually grow as they see results. Manufacturing facilities are able to transform artificial intelligence insights into actionable plans without having to completely remodel every process overnight if they integrate predictive maintenance into their current ERP and maintenance management systems.
An era in which breakdowns are very uncommon
A future in which unexpected equipment failures become the exception rather than the rule is the goal that is driving the use of artificial intelligence in manufacturing. Rather of responding to issues as they arise, factories operate in a proactive manner, backed by real-time insights that ensure the health of machinery and the smooth functioning of activities.
It is possible that as technology advances, predictive maintenance systems may have the ability to provide recommendations for process improvements, to balance machine workloads, and even to automatically trigger orders for replacement components when excessive wear is identified. Aside from being a tool for maintenance, artificial intelligence has the potential to become a partner in the management of efficiency, quality, and sustainability.
The Evolution of Maintenance from a Cost-Based to a Value-Based Perspective
Predictive maintenance that is powered by artificial intelligence is not just a technological advancement; it signals a revolution in the way that manufacturers think about the upkeep of their equipment. Downtime is turned into uptime, operating expenses are reduced, and factories are able to function more efficiently and safely as a result of improving their ability to detect issues before they occur. In a sector where every minute is of the utmost importance, predictive maintenance provides a significant advantage. It demonstrates that when machines and algorithms collaborate, the end result is not only a reduction in the number of failures, but also a manufacturing future that is more robust and competitive.